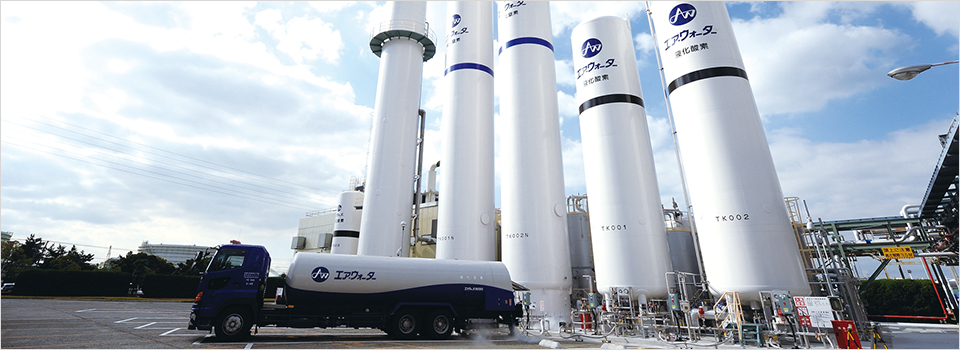
We use our expertise in process engineering for cryogenic air separation — the core technology of the industrial gas business — and in the design, manufacture, construction, safety management, and maintenance of industrial gas production equipment, piping equipment, and various gas applications. This is part of our consistent approach to development.
We are constructing an engineering system capable of responding to the international expansion of the Air Water Group, the robust increase in production by major semiconductor manufacturers, and the increased scale of equipment.
We engineer gas production equipment and gas supply facilities used in the construction of new plants and the expansion of existing plants. We provide comprehensive engineering expertise related to the design, construction, maintenance, safe operation, and quality control of various gas generators. These include cryogenic air separators, highly efficient and compact liquefied oxygen/nitrogen co-production plants (VSUs), nitrogen gas generators (V1 series), PSA-type oxygen gas generators (VP series), and hydrogen generators (VH series). Our expertise encompasses our unique technologies in the areas of adsorption, membrane separation, reaction, and purification.
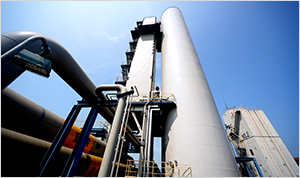
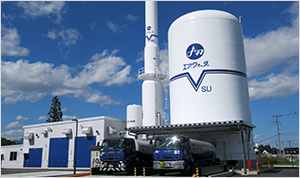
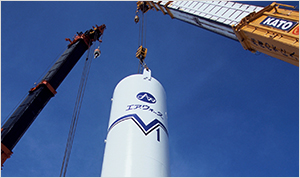
Our cryogenic and high-vacuum technologies are indispensable to the safe and stable supply of industrial gases. We design and construct low-temperature liquefied gas carriers (LGCs), low-temperature liquefied gas storage tanks (known as cold evaporators, or CE), low-temperature liquefied gas trucks, vacuum-insulated piping, centrifugal pumps, and air-temperature evaporators, which are essential for the delivery and use of industrial gases. We remain focused on the development of proprietary technologies and innovative products that utilize control technologies for temperature ranges approaching absolute zero.
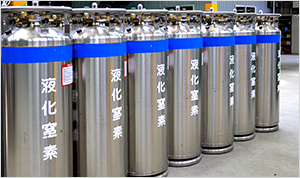
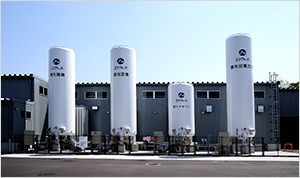
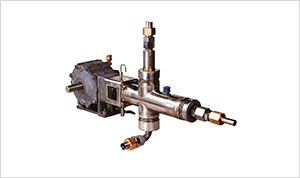
Manufacturers of electronic devices such as liquid crystals, solar cells, and semiconductors require a dependable supply of high-purity gases. We devise and manufacture products with strict quality control measures by using the piping and welding expertise acquired through our many years of hands-on experience. We offer supply piping for bulk gas and special gases, purification equipment, cylinder cabinets, abatement equipment, gas alarm systems, and gas analysis systems. These offerings demonstrate our commitment to providing safe and stable gas supply systems.
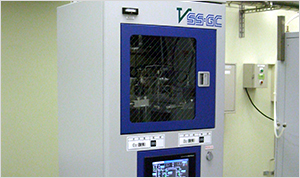
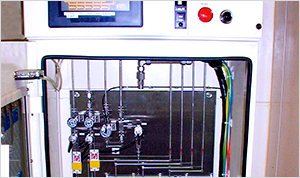
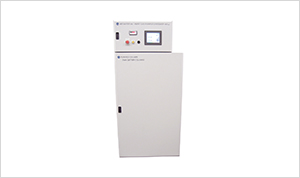
Energy conservation and reduced dependence on petroleum are being encouraged in response to the growing transition to a low-carbon society. As part of this effort, conversions from petroleum-based gases to liquid natural gas (LNG) are being promoted. We manufacture LNG tank trucks and shipping containers and design and construct storage tanks and LNG satellite facilities to support this transition. In addition, we are combining cryogenic technology with the proprietary expertise we have developed over many years to apply existing technologies while we actively develop new innovations.
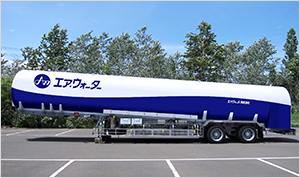
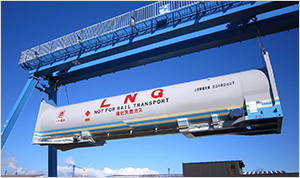
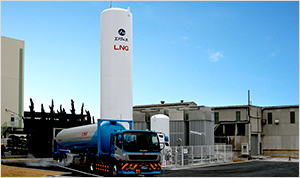
By effectively utilizing the unique characteristics of industrial gases, we develop, design, and construct gas-fueled equipment and devices that contribute to production efficiency and technological advancement.
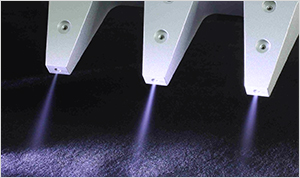
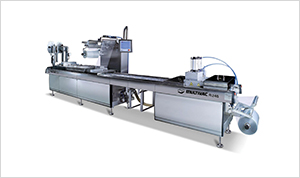
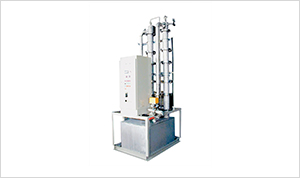
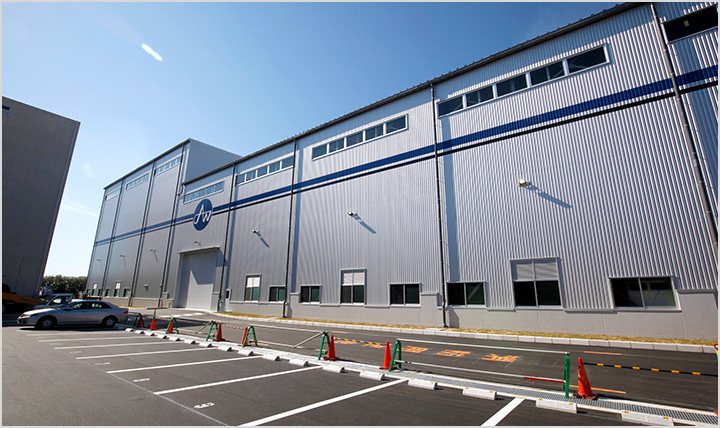
The high level of expertise, skills, technologies, and design know-how this plant has accumulated in the manufacturing realm enables it to produce air separation plants, various gas generators, and CE and industrial gas equipment.
In addition to manufacturing large-scale equipment, this plant also produces a large number of gas supply units for the production of semiconductors, liquid crystals, LNG-related equipment and rocket-related equipment. The Sakai Plant continue to strengthen its manufacturing facilities in order to meet increasingly diverse customer needs.
- Total floor area 3,700 square meters
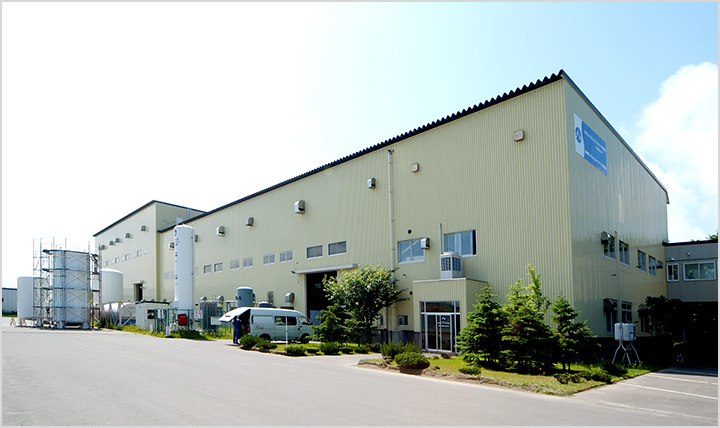
Thanks to its advanced cryogenic technologies, this plant is capable of producing large containers, vacuum-insulated piping, artificial air-generating systems, gas supply units, and other equipment related to LNG containers and low-temperature liquefied gas trucks. In 2015, this plant developed and shipped Japan’s first marine vessel fuel supply facility for the Sakigake, an LNG-fueled tugboat.
- Total floor area: 2,700 square meters